ABSTRACT: In the dynamic offshore energy landscape, transformer reliability is important as governments, institutions and utilities around the world pursue sustainable energy goals. While green energy initiatives reduce dependence on fossil fuels, they introduce complex options such as transitioning to ester transformer fluids and dry transformers. Incidents such as the EQUINOR Asgard B platform fire highlight the underestimated risks. The design of ester fluid transformer installations is complex, with potentially costly delays. To meet these challenges, offshore projects, including the Neart Na Gaoithe Offshore Windfarm, choose the TRANSFORMER PROTECTOR™ system, which ensures the safety and stability of power production in a changing marine environment.
In the ever-evolving landscape of offshore operations, where energy production meets the boundless horizon of the open sea, the reliability of transformers is a paramount concern. These critical components ensure the seamless transmission of electrical power, making them the silent heroes of offshore platforms and substations. In the global pursuit of sustainable energy and emissions reduction goals, governments, institutions, utilities, and agencies have turned to a variety of tools and protocols as their multiple means of charting a greener future.
Green energies are reducing dependence on fossil fuels worldwide, and power transformers play a vital role at the heart of this movement. For example, the switch from mineral oil to ester transformer fluids and the use of dry transformers in some projects of renewable energies reflect a trend towards sustainability in all industrial sectors.
However, often, performance and operating costs are often ignored, and the consequences of failures and malfunctions are sometimes underestimated.
Sometimes, however, these changes do not bring the environmental protection that was expected of them, but instead produce the traditional problems, unintended consequences and environmental damage that would have been experienced if these measures had not been taken. This is the case of the failure of an internal transformer when a short circuit creates an electric arc that pressurizes the tank and triggers an explosion and subsequent fire and smoke. When this “arc” reaches 2000C°, a temperature above the flash point of any oil or ester fluid, at this stage (which could occur in milliseconds) the rupture of the tank is inevitable, a large amount of “liquid” will be poured over the ocean and a smoke will diffuse into the atmosphere from the transformer giving the impression of environmental pollution.
An incident to illustrate this had happened on Asgard B platform of EQUINOR in November 2022 when, as result of a short circuit/arc a transformer caught fire. The results of this incident:
- Petroleum Safety Authority of Norway (PSA)investigations on site. With one nonconformity and two improvement points.
- Transformer breakdown and consequent loss of production.
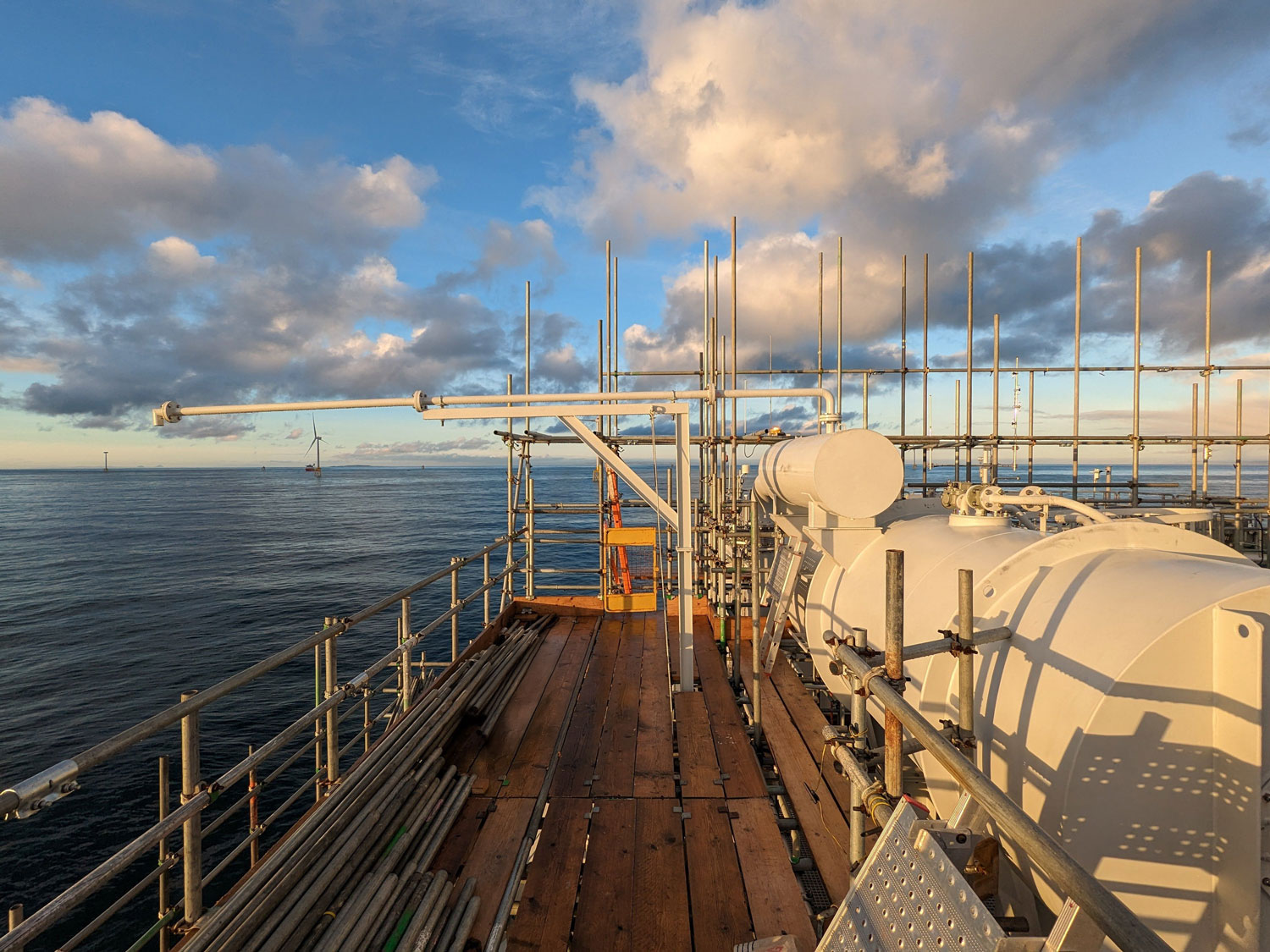
EQUINOR was using for this site a dry-type electrical transformer with a higher operational cost, and a less efficient performance vs an oil-filled transformer, based on the common assumption that dry transformers were safer and less pollutants, and maybe better adapted to offshore operations. On its Report the PSA conclude that “The direct cause of the fire in the transformation is a short circuit/arc flash resulting from impairments to and/or degradation in the winding insulation over time. 1”
TAKEAWAY LESSON:
In offshore installations, whenever low impedance faults occur, a transformer explosion is on the verge of occurring, causing smoke, ocean debris and fires as an immediate consequence. And loss of production and on-site investigations for the asset owner.
Another common assumption about transformer types for offshore applications is the belief that synthetic oils, often seen as environmentally friendly alternatives, are inherently safer and their commissioning is smooth and summary. However, as we delve deeper into this complex matrix of options, it becomes clear that the story is far from straightforward.
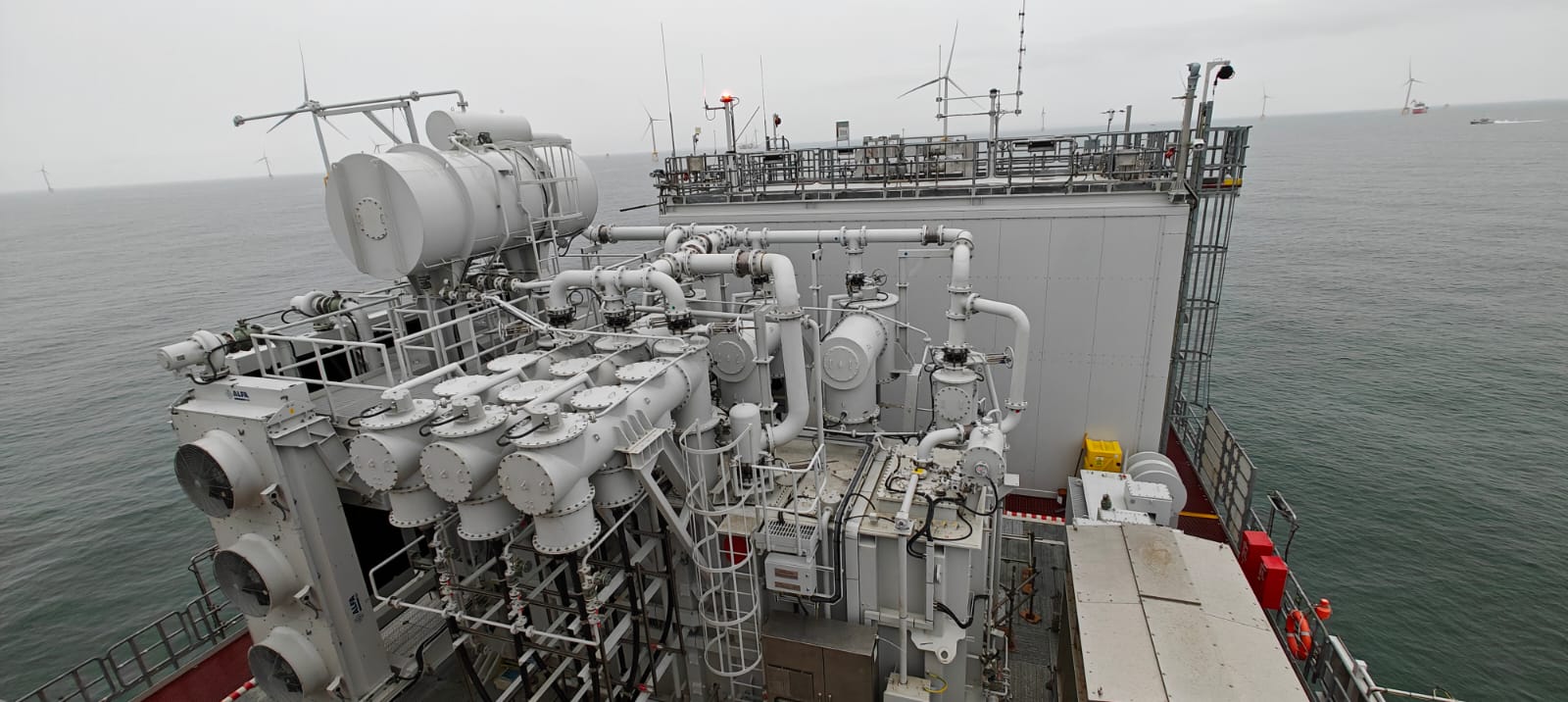
Typically, the design process of the ester fluid transformer installation is different and more complex to perform. In addition, during type testing and environmental permitting, problems could arise, and the solution would be costly and take months, impacting the project lead time; to put a figure on it, for one project the amount could skyrocket to millions of dollars a day combining penalties and production losses.
On the project planning and the specificities of the offshore installations the International Renewable Energy Agency IRENA in their Report “Renewable Power Generation Cost 2022” indicates: “Unlike onshore wind projects, offshore wind farms must contend with installation, and operation and maintenance (O&M), in harsh marine environments, making these projects costlier and giving them significantly longer lead times. The planning and project development required for offshore wind farms is therefore more complex than that for onshore wind projects. Construction is even more complex again, increasing total installed costs still further. Given their offshore location, these projects also have higher grid connection costs. 2”.
Many offshore facilities like Neart Na Gaoithe Offshore Windfarm, a 450 MW offshore wind farm located off the Fife coast of Scotland, took a different approach on these matters and choose to install the TRANSFORMER PROTECTOR™ system on the transformer’s fleet of the substations attached to the windfarm.
By choosing SERGI Transformer Protector, EDF Renewables and ESB secured their substation transformers protecting them from explosions due to short circuits, preventing fires, water contamination and ensuring stable power output.